To |
Mohamed Misbah |
Company |
Forsan Foods & Consumer Products Co. Ltd |
Country |
Saudi Arabia |
File NO. |
LY-20200529001BY |
Date |
20200529 |
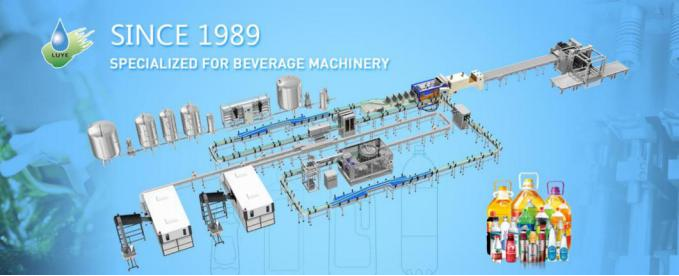
Aluminum Can Carbonated Beverage Drink Filling Production Line
With Capacity 2000BPH (320ml)
(PROPOSAL DETAILS)
Contact: Bobby Liu
Mobile phone/Whatsapp: +8613773224489
E-mail: bobby@lymachinery.com
This proposal is preliminary, subject to final agreement after technical and commercial communication.Period of Validity: 3 months.
Flow Chart
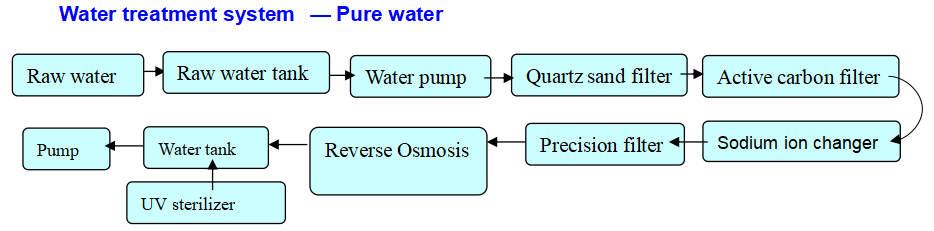
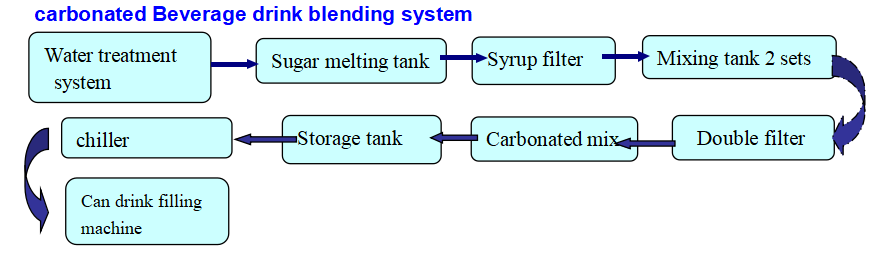
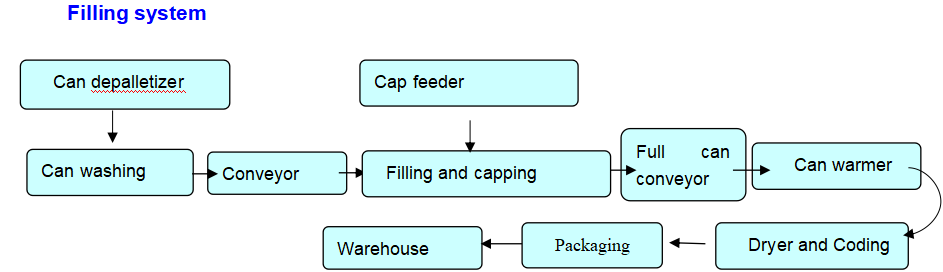
Ⅰ, Equipment & Price List
Ⅱ, MACHINE DESCRIPTION
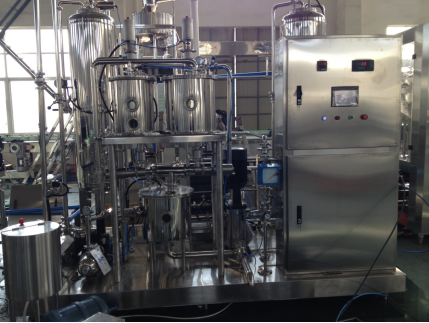
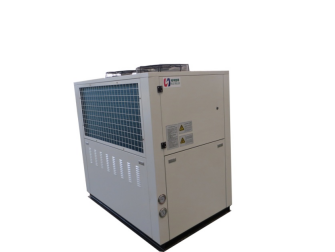
1.Carbonated Drink- Blending&Mixing system
A) Air cooled box type chiller
QHS2000 series drink mixer structure reasonable, the mix precision is high, CO2 mixes fully, has two times of cooling, two carbonation merits. Mainly is suitable for kinds of carbonic acid drink's mix processing, also may use in the paste drink, the fermentation drink and so on other soft drinks' mix processing.
B) CHARACTERISTIC
1. Material excellent, the processing is precise:
Every selects the high quality stainless steel manufacture with the drink contact spot, the inside、outside surface passes through precisely polishing processing, completely conforms to the international food requirement.
2. Automaticity high, the movement is stable:
This machine through the microcomputer control production operation entire process, the movement is stable; if breaks down, the alarm device can prompt and the automatism stop.
3. The ease of operation, easy to adjust:
This machine operation is starting button in turn according to the stipulated procedure, then realizes the normal operation; Does not need to replace any spare part, namely can very conveniently adjust the productivity or mixture ratio of the water and sugar.
4. Mixes evenly, the proportion is accurate:
Because uses the disposable mix the advanced craft, therefore the mix is even; proportion of the water and the syrup mixture is controlled by the fine tuning function measurement installment strictly, its mix precision may achieve about 5/1000
5. The CO2 content is high:
This machine uses the vacuum deaeration, the deaeration rate reaches as high as above 90%; Has the deaeration, the carbonized two cooling function, has the function which two time carbonizes, Therefore air content is specially high, usually may achieve 3.5 ~ 3.8 time or higher somewhat.
6. The structure health, easy to clean:
This machine uses the loop system which the stainless steel makes, has satisfies the CIP home position purifier carries on to the equipment and the pipeline disappears the venom and the hot water clean ability; This machine production drink, each milliliter bacterium reproduction rate < 5%, the Escherichia coli is zero.
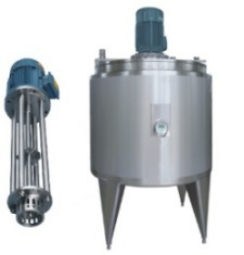
C) High speed melting tank
Stainless steel SUS304, internal bladder δ3mm, mile board is δ1.5mm, external stainless steel board is δ1.5mm, and polyamine foam insulation, complete closed、vertical syrup stirring, 60r/min、digital temperature gauge、motor power is 1.1KW. Washing head 、material outlet at bottom is Ф38 and breather.
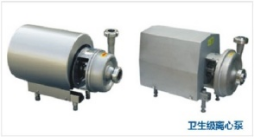
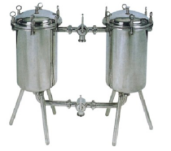
E) Beverage Pump
The contact part with materials, pump housing, impeller, nut and support foot are made of stainless steel 304 material, and the sealing ring is made of food hygiene rubber and hard alloy sealing ring.
D) Bag-type Duplex Filter
Made of stainless steel 304, double balanced structure, with 100 mesh stainless steel mesh inside, the filter screen can be replaced without shutdown.
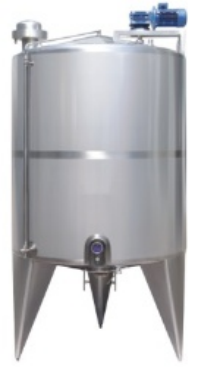
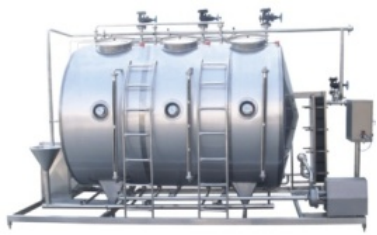
F) Beverage Pump
The contact part with materials, pump housing, impeller, nut and support foot are made of stainless steel 304 material, and the sealing ring is made of food hygiene rubber and hard alloy sealing ring.
G) CIP system
The tank body is made of SUS304. The thickness is 3mm. Acid and alkali tanks are provided with insulation layer.
The inner and outer welds of the tank body shall be polished. There is no sanitary dead angle inside the tank for easy cleaning.
The tank body is equipped with a glass liquid level gauge, a dust-proof respirator, a liquid inlet, a liquid outlet, a drain outlet, a sampling valve, a quick installation sanitary manhole, etc.
Adjustable level of legs.
2. Aluminum Can Carbonated Water filler & packager
A) Empty cans depalletizer
Pop can empty can depalletizer is the mainly suitable for automatic depalletizing of the complete piles of the empty cans. It hoists the empty cans palletized on the pallets layer by layer from bottom to top and then them to the conveying chain-plate. Used together with the empty can spraying washer, it can replace the manual ways arrangement and traditional empty can unloading machine, saving a lot of manpower and increasing production effects.
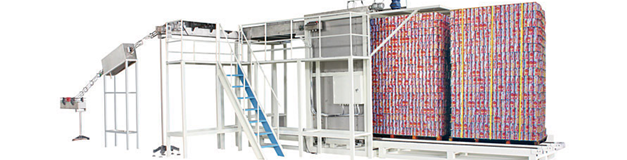
During the period of work, the forklift puts the pallets where empty cans are palletized onto the pallet conveyor, and the conveyor will carry them to the pallet lift platform of the main machine. The pallet lift platform is used to send the positioned empty cans to the can unloading height. When the empty can cans are unloaded, the empty pallets will fall and be put onto the conveyor. All the rising and falling actions are controlled by the self-locking lift system device. The rising or falling speed can be separately adjusted to meet the operation need. During the empty can unloading, the motor drives the chain wheel and chain device to push the cans, and then the full piles of the empty can will be pushed onto the net conveyor, and will return to the preparation position and continue to push out the next pile. All action positioning is controlled by the photoelectric switch. The can unloading with continuous actions or single circulating mode can be selected.
The pallet feeding direction, can discharging direction and operation panel position of the machine can be flexibly changed according to user requirement.
Main technical parameters:
Production capacity: 30~400can per min
Power: 3.5kw
Weight: 2500kg
Dimension: 7000*4500*3500mm
B) Slideway can washer
The front can turning- over cutter cage of the washer is connected with the rapid transportation of the can loading turn-table. The empty cans that come from the can turning-over machine have a 180°turn. Then the can entering the washing tank of the empty can wash by the opening downward. The back of the tank is the drain part. The water, which sprayed into the empty can flow back the tank, then the wastewater discharged by the discharge pipes. After cleaning the empty can have a 180°turn by the back can turning-over machine, then the can entering the feed conveyor belt by opening upward.
Main technical parameters:
Production capacity: 30~400can per min
Weight: 150kg
Dimension: 4000*500*2300mm
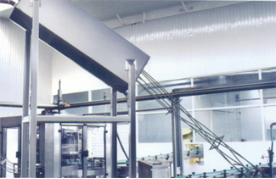
C) Can Filler/Sealer
The monoblock is composed:
FILLER-SEALER
General Introduction:
It is suitable for filling and capping carbonated drinks such as cola, carbonated water etc. It is equipped the advanced device, electrical equipment, and pneumatic control technology. It has the characteristics of filling reposefully, high speed, liquid level control, capping reliably, frequency conversion timing, less material loss. It can be equipped long-distance control system. It is the preferred equipment for the medium beer and beverage plant.
Main Features:
● Wholly sealed widow structure which is beautiful, concise, easy and highly operated;
● Cycling tank design with precision polishing inside;
● High precision and large flow rate filling valves to meet productive requirement;
● Specially designed roller structure which is easy to be adjusted, locked and ensure sealing function;
● Friendly and convenient operating panel with high expansibility.
● The filling valve is adopts high precision mechanism valve, fast speed filling, high precision liquid level.
● The filling vat adopts 304L material designed sealing vat, to achieve constant pressure filling.
● The flow rate of the filling valve>125ml/s.
● Main transmission adopts toothed belt and gearbox open-type transmission assemblies, high efficiency, low noise.
● The main drive adopts step-less speed change for frequency conversion, the whole machine adopts PLC control; the capping machine and filling machine adopt coupling joint, to ensure synchronization of two machines.
● With filling with can, no filling without can.
● The filling manner is constant pressure filling, with fast filling speed and stable action.
● Adopting introduce into full set of Switzerland (Ferrum) capping technology.
● Capping trolley adopts high hardness alloy steel quench(HRC>62), capping curve adopts projection grinder precision machining, to ensure the quality of capping.
● With capping with can, no capping without can control system, to ensure the normal running of the machine.
● With CIP automatic rinsing function.
● With centralized lubrication system.
Working Procedure:
Can will be pushed into can holding platform one by one by feeding screw and star-wheel. Centering cup of filling valve will fall to can; the distance between filling valves and cans is sealed by springiness plastic ring. The movement of centering cup is generated by plastic idler wheel along curvilinear motion. After filled, valve will be closed, air is discharged, and centering cup will rise from the can. Filled can will be sent to conveyor chain, then to capper. Capper will take cap, turn over the edge of can and turn the edge to finish the sealing action by the control of cam. After that can will be transferred to conveying system.
Main Specifications:
1. Material of filling valve: Stainless steel SUS304
2. Material of rotary tray and machine platform: Stainless steel SUS304.
Accessories brand
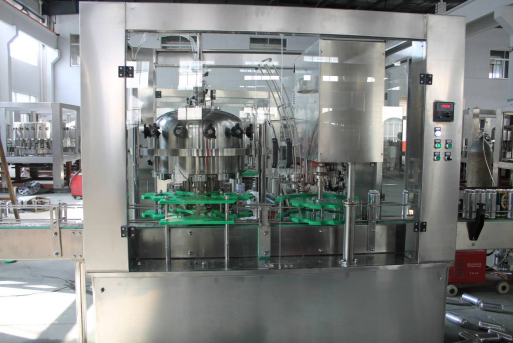
D) Warm machine
This continuous sterilization machine is newly designed and manufactured by introducing the advanced foreign technique. It is used for sterilizing kinks of food products, such as plastic/glass bottles juice and beer, tin can and aluminum can juice under ordinary pressure, and even for cooling the hot filling tea and juice drinks and warming the low temperature filling carbonated-soft drinks.
This machine is combined by the circled hot water spraying, warm water pre-cooling, and warming cans segments that can get better water and energy conservation. All of the cans will be carried in and out automatically, and the line would be achieved full automatically. The whole body of the machine is made of 304stainless steel; in addition the machine has a good appearance, smooth running state and simply operation.
Model: BWPS
Material:SUS304 Stainless steel
Input: stainless steel water flume
Water pump:1-25T/H
Overall dimension: 8000m
Weight: About 2800kg
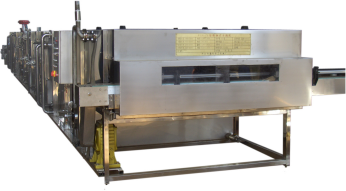
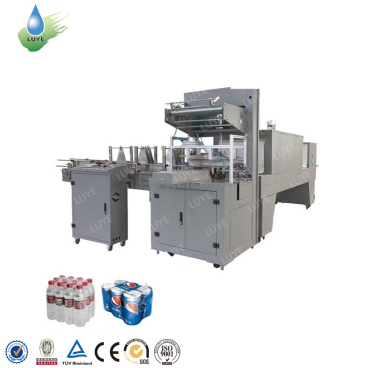
E) PE Film Shrink-wrapping Machine
Applications:
1. Model: LYBS6545auto film wrapping machine
LYBS 6545 auto film wrapping machine is designed and manufactured based on the latest technology,for the demand of packing requirement of beverage production, as pure water,mineral water,juice,soft drink,etc. It is automatic wrapping, with shrink tunnel,packed perfectly.
2. Features of LYBS 6545 auto film wrapping machine
1) Automatic sorting conveyor system, which has the guiding separating stainless steel tube and the sorting plate making the bottles in standard roll for the wrapping purpose, to make sure that the group of bottles of 3 x 4, 4 x 6, or 2 x 6, 4 x 5 pcs of bottles in place for the wrapping need.
2) Automatic PE membrane processing part, which contains the upper and lower roll-feed PE membrane system in place and equipped with automatic infra-red sensoring system for checking the group of bottles being ready for wrapping and cutting sealing, the whole process is to be done instantly by the PLC control system.
The wrapped bottles will be pushed into the shrinking tunnel conveyor by the automatic pushing system, which pushes the wrapped bottle onto the conveyor of the shrinking tunnel.
3) Automatic hot wind shrinking tunnel, the shrinking system is the separated part of the machine has the separated controlling unit for the temperature controlled by touch screen temperature controlling system.
4) Touch screen control panel with PLC and electrical control system.
F) Filled bottled Conveyor System
Main features:
1. Stable conveying, using synchronous chasing control between the conveying belt and engine, making bottles in good condition in the conveying: non-falling, non-block, non-jam. And the cushion platform can be set before labeling machine, when the label is changed, the filling machine can keep working, no need to stop and waiting. The filled product during this period will be stored by the cushion, when label changing is finished, labeling machine will label the stored product in a high speed, and producing speed recovered.
2. Conveying belt is designed by module, component can be interchanged easily, structure is compact, noise is little, easy assembling and maintaining, have flexibility to combine the bottle type according to the different capacity.
3. The design of electrical control is advanced and rational, we can design the control method, select the electrical control component according to client’s layout, to improve the conveying stability.
4. Switch according to conveying system layout or customer reasonable requirement, for the convenience of operation.
5. Belt lubricating system is equipped
6. Main part all using SUS304.
7. Fringe board is using the U.S. Rexnord technology to produce.
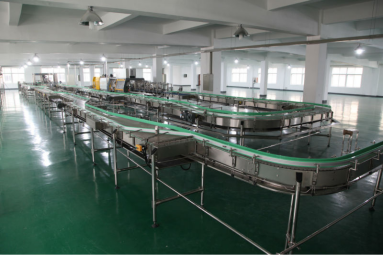
Post time: Nov-30-2022